Технический обзор мощностных стендов
Технический обзор
Стараясь усовершенствовать технологическую сторону измерений, железнодорожные инженеры в 18 веке использовали водяные тормоза все большего размера для своих стационарных роликовых динамометров. На сегодняшний день также существует целый спектр технологических возможностей для применения управляемого торможения вращающихся валов. Тем не менее, на практике применение нагрузок такого типа на ходовую часть транспортного средства ограничивается несколькими техническими вариантами. Далее мы дадим небольшой обзор нескольких основных принципов.
Измерения крутящего момента и частоты вращения, необходимые для расчета мощности, могут быть произведены различными способами. Ниже приведено описание системы измерения силы при помощи тензодатчиков.
Тензодатчики
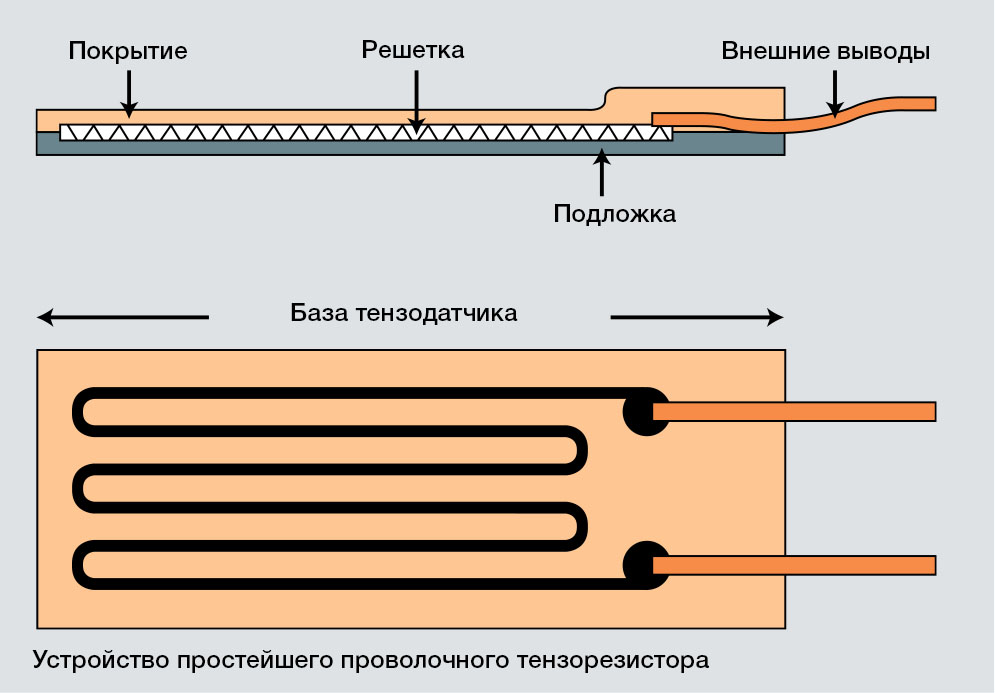
Типичный проволочный тензодатчик состоит из подложки, на которой размещен активный чувствительный элемент (решетка из сверхтонкой проволоки с высоким электрическим сопротивлением).
Тензодатчик устанавливают на высокочувствительный элемент конструкции при помощи специального клея.
В зависимости от размеров тензодатчиков и способов их включения в электрическую измерительную цепь (обычно это мост Уитстона, или полностью термокомпенсированный тензомост), можно создать целый ряд конструкций датчиков силы.
Тормоза
Гидрокинетические системы
Гидрокинетические тормоза динамометров (далее просто гидравлические тормоза) это в действительности не что иное, как хорошо знакомые гидромуфты классической автоматической трансмиссии. Это устройство увеличивает передаваемый крутящий момент в зависимости от числа оборотов и нагрузки посредством турбины с обгонной муфтой.
Но с другой стороны, гидравлические тормоза не используют дополнительное отклонение потока жидкости и поэтому они ближе к гидравлической муфте, изобретенной Фёттингером, чем к гидротрансформатору с реактором, установленным на муфте свободного хода.
История Создание первых гидродинамических передач связано с развитием судостроения в конце XIX века. В то время в морском флоте стали применять быстроходные паровые турбины, что вызвало необходимость понижения оборотов вала до скорости вращения гребного винта в пределах 200—300 об/мин или ниже — на крупногабаритных судах, т.к. наиболее высокий КПД гребных винтов проявляется именно в этих пределах. Кроме этого, высокие обороты вызывают кавитацию на лопастях и большие нагрузки. Это потребовало применения дополнительных механизмов. Поскольку технологии в то время не позволяли изготавливать высокооборотные зубчатые передачи, то потребовалось создание принципиально новых передач. Первым таким устройством с относительно высоким КПД явился изобретённый немецким профессором Г. Фётингером гидравлический трансформатор (патент 1902 года), представлявший собой объединённые в одном корпусе насос, турбину и неподвижный реактор. Однако первая применённая на практике конструкция гидродинамической передачи была создана в 1908 году и имела КПД около 83%. Позднее гидродинамические передачи нашли применение в автомобилях. Они повышали плавность трогания с места. В 1930 году Гарольд Синклер, работая в компании Даймлер, разработал для автобусов трансмиссию, включающую гидромуфту и планетарную передачу. В 1930-х годах производились первые дизельные локомотивы, использовавшие гидромуфты. |
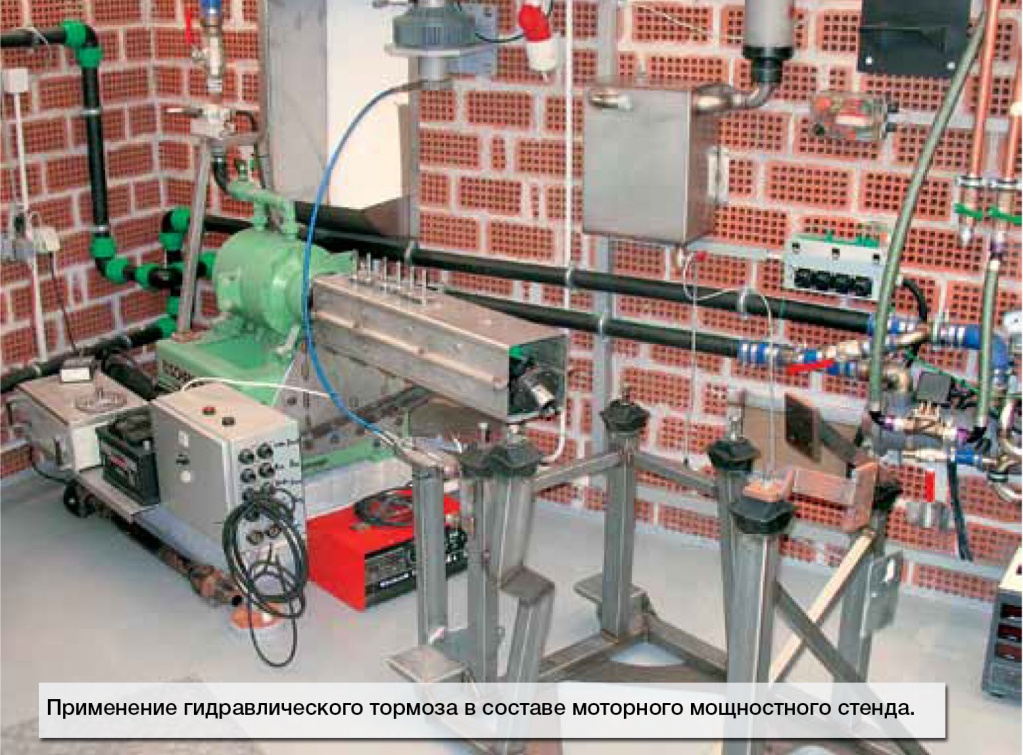
Для всех гидравлических тормозов действует один основной принцип, хотя имеется две базовые версии в зависимости от конструкции: тормозная эффективность двигателей с постоянной производительностью (закрытая система) может быть отрегулирована при помощи сменных управляющих дисков между ротором и статором. Специфические отверстия в этих регулировочных дисках могут избирательно воздействовать на поток жидкости, а с ним и на преобразование энергии и эффективность работы тормозной системы. В других версиях эффективность тормозов регулируется потоком жидкости, подаваемой в гидравлические тормоза через клапаны на впуске и впуске гидравлической схемы (открытая система).
Главное преимущество гидрокинетической системы по сравнению с остальными тормозными системами - это сравнительно низкая стоимость. Именно это обусловило ее широкое применение. К тому же, возможно сделать гидравлический тормоз практически любого размера. И даже гигантские размеры довольно просто воплотить в жизнь. Однако, есть несколько существенных недостатков в сравнении с современным электродинамическим тормозом. Даже в открытой системе точная модуляция гидравлических тормозов обычного типа зависит от многих потенциальных возмущающих переменных. Конструкция динамометра с его гидравлическими, механическими и электрическими частями обходится довольно дорого по причине сложных требований к регулированию и управлению системой. В целом это делает гидравлические тормоза более подверженными различным дефектам и ошибкам. Проблемы с коррозией, кавитацией и эрозией можно исключать только при высоком уровне конструирования, большой стоимости производства и затрат на техническое обслуживание. К этому можно добавить, что характеристики чувствительности гидравлических тормозов в принципе хуже, нежели чем, например, у индукционного тормоза, а их системы регулирования и управления гораздо сложнее автоматизируются.
Благодаря долгой истории развития гидрокинетических тормозных систем на сегодняшний день существует множество вариантов реализации данной технологии. Но в любом случае даже самые простые системы должны развиваться в более сложные системы, чтобы быть способными отвечать современным требованиям.
Гидравлическая муфта
В случае с простой гидромуфтой гидравлическая передача крутящего момента и мощности на вращающиеся валы достигается только при помощи ротора и статора в общем корпусе турбины. Ротор, соединенный с коленвалом двигателя, приводит в движение жидкость, находящуюся в корпусе. Кинетическая энергия жидкости передается на колесо статора, которое соединено с ведомым валом. В данной ситуации не возникает ни механического трения, ни перегрузки по крутящему моменту. Эффективность в большей степени зависит от разницы частот вращения ротора и статора, но не может достигнуть 100 % без дополнительной механической блокировочной муфты.
Инерционные системы
Инерционные тормозные системы в динамометрах (часто используется название «инерционные динамометры») обычно нагружают привод автомобиля посредством инерции своих вращающихся масс. Факт того, что необходимы дополнительные силовые затраты для изменения конкретного состояния вращения маховика, еще раз подтверждает, что данная технология физически устарела. Современные процедуры измерения мощности и экологических показателей под нагрузкой, давно уже не ограничиваются измерением лишь максимальной мощности. Тем не менее, в чистом виде инерционные динамометры предназначены именно для этого, или, другими словами: на динамометре, работающем по этому принципу, вы ничего более измерить не сможете.
Однако многие динамометры имеют одну или несколько отдельных центробежных масс. Само собой разумеется, что согласно закону инерции, динамометры такой конструкции не могут ни приложить усилие на постоянной скорости и измерить мощность, ни воссоздать реальный цикл езды с различными нагрузками. По этой причине часто можно видеть попытки скомбинировать обе рассмотренные системы в одном динамометре используя комбинацию из маховиков – преобразователей и, например, индукционных тормозов или электродвигателей постоянного тока.
Несмотря на фундаментальные конструкционные компромиссы, возможность применений таких гибридных концепций вполне допустима для определенных целей.
Например, во многих странах, проверка выхлопных газов на транспортном средстве под нагрузкой на таких динамометрах было регламентированной практикой многие года. Даже старомодная "классическая" автомобильная техника может быть проверена до определенного уровня требований с использованием гибридных инерционных динамометров. Современные же транспортные средства, оснащенные сложными мехатронными системами, требуют применения соответственно таких же сложных динамометрических технологий, которые мы рассмотрим в дальнейшем.
Такая ситуация складывается потому, что в случае некоторых повреждений – назовем в качестве примера турбокомпрессор VTG, регулирующий клапана - часто проявляются только минимальные симптомы, которые обычной технологией измерений сложно определить.
VTG (Variable Turbo Geometry) турбокомпрессор с изменяемой геометрией -
Турбокомпрессор с изменяемой геометрией позволяет регулировать давление наддува для любых рабочих режимов. Потребление топлива и объем выхлопных газов могут быть снижены, что позволит оптимизировать и улучшить характеристики мощности и крутящего момента.
Выявление таких ошибок на сегодняшний день является реальной задачей для современных высокотехнологичных мощностных стендов. Далее мы рассмотрим примеры диагностирования таких ошибок. Однако именно из-за своей инертности вращающиеся центробежные массы не могут выявить мизерные отклонения, такие, например, как неправильная установка распределительного вала. К тому же они не обладают достаточной возможностью быстро и точно изменять нагрузки. Чем больше вращающие массы, тем сложнее соответствовать этому требованию. Даже только по этой причине мощностные стенды, работающие по принципу инерционных масс, не могут удовлетворять потребностям индустрии автомобильной диагностики.
Электродинамический тормоз и электромоторы
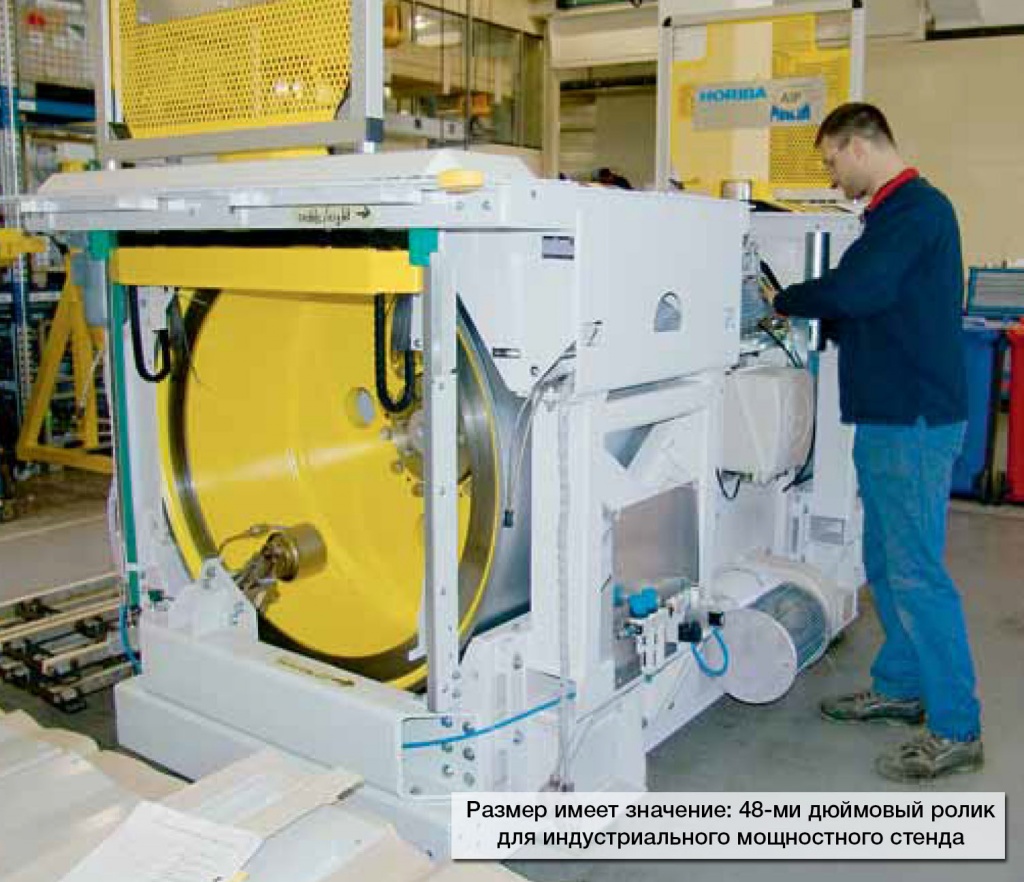
Электродвигатели переменного и постоянного тока в мощностных стендах могут использоваться как для привода так и в качестве генераторов торможения. Двигатели постоянного и переменного тока можно также комбинировать; обычно двигатель постоянного тока выступает в качестве приводного, а переменного - в роли элемента, обеспечивающего торможение. С учетом достаточной сложности такая комбинации моторов переменного/постоянного тока может быть очень эффективной и гибкой. Из-за размеров таких систем и высоких соответствующих затрат, они используются в основном в автомобильной промышленности. В стандартных динамометрах электромоторы обычно применяются только для синхронного привода ведомых осей.
В целом электродинамические тормоза (ЭДТ) наиболее подходят для мощностных и экологических испытаний на современных динамометрах в неиндустриальном автомобильном секторе.
Они используют принцип электромагнитной индукции для создания крутящего момента на ведущих колесах транспортного средства и, как следствие, обеспечивают селективное торможение. Аксиально расположенные катушки создают магнитное поле, в котором вращаются дисковые металлические роторы, подсоединенные через муфты к роликам стенда. При вращении в роторах индуцируется ток и создаются вихревые токи. При вращении они создают свои собственные магнитные поля, которые работают в противоположном оригинальному полю направлении.
Поскольку электрическое сопротивление металлических роторов составляет резистивную нагрузку, кинетическая энергия трансформируется в тепло: транспортное средство тормозится. Тормозная эффективность может легко регулироваться с высокой степенью точности посредством подачи управляющего напряжения на катушки. Электродинамические тормоза в мощностных стендах обычного типа обеспечивают высококачественную (стабильную и устойчивую) мощность торможения до 1000 кВт. Электроника полностью компенсирует отклонения кривой мощностных показателей из-за потерь обусловленных температурными факторами, потерь, вызванных трением в подшипниках и т.д., таким образом, что система выдает в высшей степени точные исправления тормозных характеристик для всего операционного цикла. Электродинамические тормоза (за исключением подшипниковых узлов) работают без трения и поэтому практически не подвергаются износу и крайне просты в уходе.
Роликовые колесные мощностные стенды (динамометры)
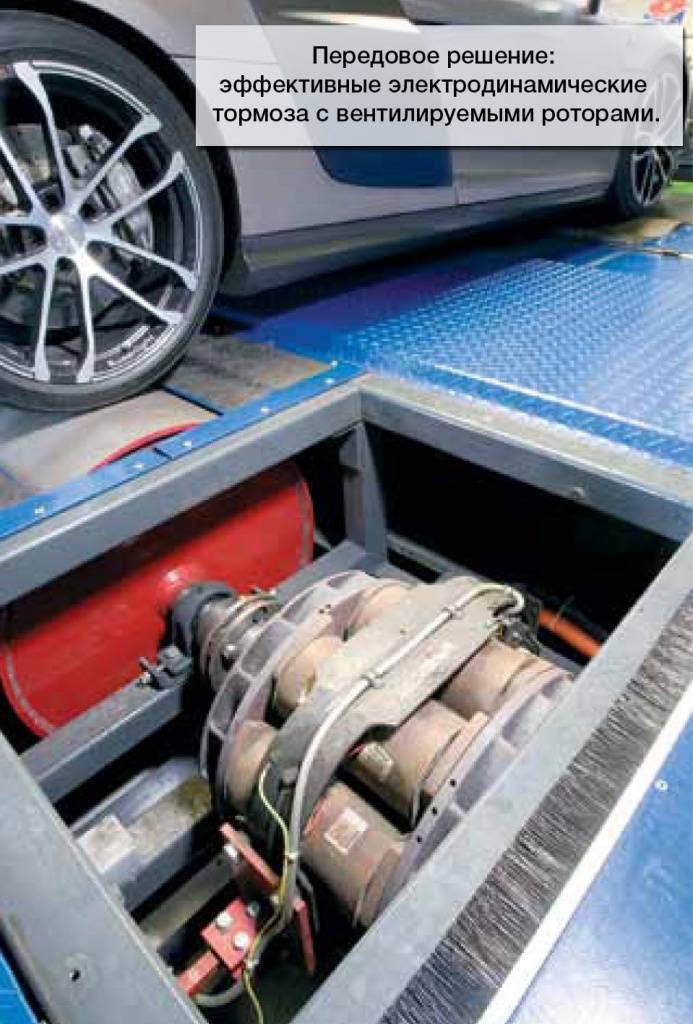
Важные влияющие факторы
Соответствующие математические расчеты достаточно сложны, поэтому более детальное описание мы здесь приводить не будем. Без них, однако, во время испытания будет учтено не достаточно влияющих факторов. Роликовый мощностной стенд поэтому должен быть способен имитировать такие реальные условия как движение в гору и накатом, а также ускорение, обгон, торможение и, что так же немаловажно, езду по бездорожью, а так же комбинацию всех данных типов движения. Единообразные условия движения по ровному дорожному покрытию это скорее исключение как в реальной жизни, так и при испытаниях на мощностном стенде.
Также необходимо принимать во внимание другие факторы, такие как ветровая нагрузка, вес, буксируемая нагрузка, давление в шинах и т.д. Очень важны потери в трансмиссии автомобиля, например, в гидротрансформаторе, различных подшипниках и, в особенности, шинах.
Следует отметить, что все эти потери имеют не простую линейную связь со скоростью или частотой вращения. Таким образом, возникает крайне сложная взаимозависимость физических переменных. Поэтому качество и, соответственно, ценность мощностного стенда определяется тем, насколько сложные алгоритмы заложены в программном обеспечении, а так же насколько он способен фиксировать и обрабатывать разные функциональные условия. Соответствующие принципы определения реальных измерений и корректирующих величин для различных условий движения будут объяснены в следующих материалах.
Ключевые особенности конструкции
Роликовые агрегаты
Одним из важнейших критериев для создания адекватной симуляции актуальных условий движения на роликовом мощностном стенде являются размеры и конфигурация роликов. Даже на сегодняшний день у простых функциональных мощностных стендов ролики обычно небольшого диаметра.
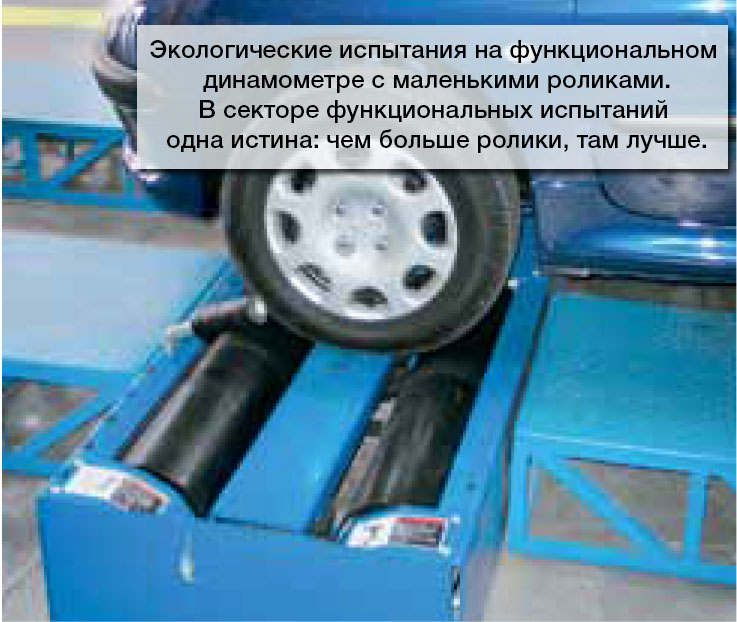
Тем не менее, поскольку в этом случае получается несоответствующий дорожным условиям контакт колеса с опорной поверхностью и, вследствие этого, сопротивление качению, они в действительности не подходят для мощностных испытаний. Для этих целей нужны ролики большого диаметра – просто для минимизации деформации шины.
В настоящее время обычная практика – применение роликов с длиной окружности 1 метр для стендов с двумя роликами под колесом. Этот роликовый агрегат включает в себя один опорный и один тормозящий ролик с колесом автомобиля, расположенным между ними. Колесо осуществляет управляемое вращение в этой роликовой призме. Кроме того, автомобиль должен быть закреплен для предотвращения выезда с динамометра.
Деформация шины и сопротивление качению
Основной причиной возникновения сопротивления качению при движении шины по дороге / шины по ролику стенда является внутреннее трение материала шины (деформация шины). Физическая теория достаточно сложна из-за различных влияющих факторов и воздействий. Важным для практики является тот факт, что сопротивление качению линейно увеличивается в арифметической зависимости от соотношения радиусов шины и ролика и определяется примерно следующим образом по формуле:
Двигатель автомобиля при испытаниях на стенде также должен преодолевать более высокий уровень сопротивления качению на ролике по сравнению с качением на дороге. Необходимо измерять мощность рассеяния или мощность механических потерь. На практике также является проблемой температура шины при мощностных испытаниях.
В автоспорте иногда устанавливают нулевые значения углов развала и схождения при тестировании с целью оптимизации тягового усилия и температурного режима за счет улучшения поверхности контакта между шиной и роликом.
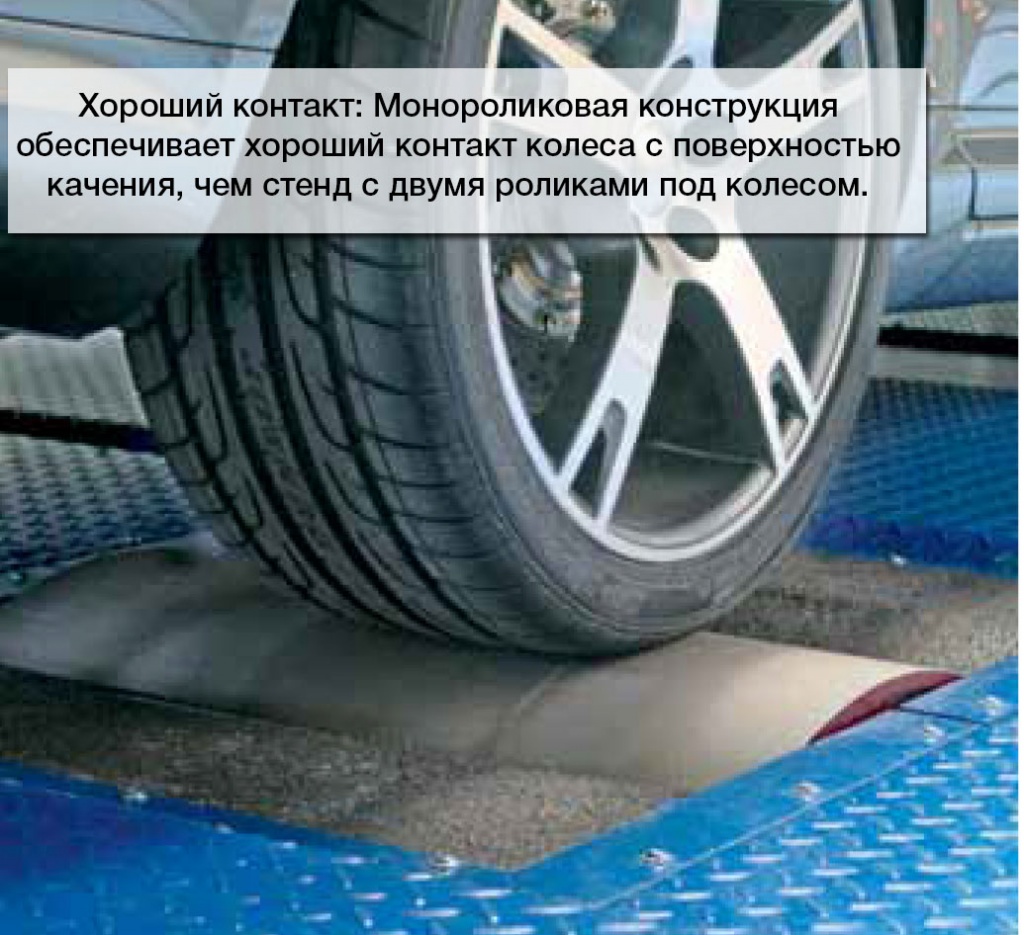
Тем не менее существует целый ряд преимуществ, если колесо находится не между двумя одинаково малыми роликами, но расположено на одном ролике большого диаметра: чем больше диаметр ролика, тем реалистичнее симуляция контакта между колесом и поверхностью качения и меньше нежелательные нагрузки, действующие на шины и, следовательно, на трансмиссию автомобиля. Верхнее расположение колеса также дает преимущество в резерве тягового усилия, что имеет особенное значение для автомобилей с высокой удельной мощностью.
Поставщики высококачественных мощностных стендов в силу всего вышесказанного имеют тенденцию выбирать монороликовые решения.
Таким образом, ролик диаметром 20 дюймов представляет собой удобный компромисс – также и в отношении конструкции. Такое положение вещей вызвано тем, что если мощностной стенд изначально установлен вровень с полом, то апгрейд до следующего поколения стенда в некоторых случаях становится проблемой. Мощностной стенд с 20 дюймовыми роликами в таких случаях все еще может быть установлен в существующий фундамент. Возникшая в некоторых случаях разница по высоте всего лишь в несколько сантиметров может быть нивелирована при помощи заездных рамп. При переоснащении существующих систем на монороликовые динамометры с большими роликами, как правило, требуется проведение работ по изменению фундаментов. С другой стороны, в случае нового монтажа, тип и размер роликового агрегата является лишь одним из многих аспектов системного планирования.
Синхронизация роликовых агрегатов
В случае многоосных динамометров есть техническое требование по обеспечению связи роликовых агрегатов, так чтобы они всегда вращались абсолютно синхронно друг с другом и что соединение было как можно более свободным от нежелательных размерных допусков и механического износа. В то же время должны быть устранены или сведены к минимуму дисбалансы во вращающихся частях и критические естественные вибрации.
Карданные валы и ременные приводы являются общеприменимыми решениями для полноприводных динамометров, потому что они являются относительно дешевыми. Однако на практике поддержание этих механических соединительных элементов в допустимом рабочем состоянии в долгосрочной перспективе сопровождается высокими затратами на техническое обслуживание. Следует учесть, что легковой автомобиль на стенде развивает скорость до 300 км/ч и выше. Возникающая при этом нагрузка на механизм передачи, независимо от его типа, огромна. Некоторые ездовые циклы, например, для симуляции определенных гоночных трасс было бы почти невозможно создать с помощью механического соединения роликовых агрегатов мощностного стенда.
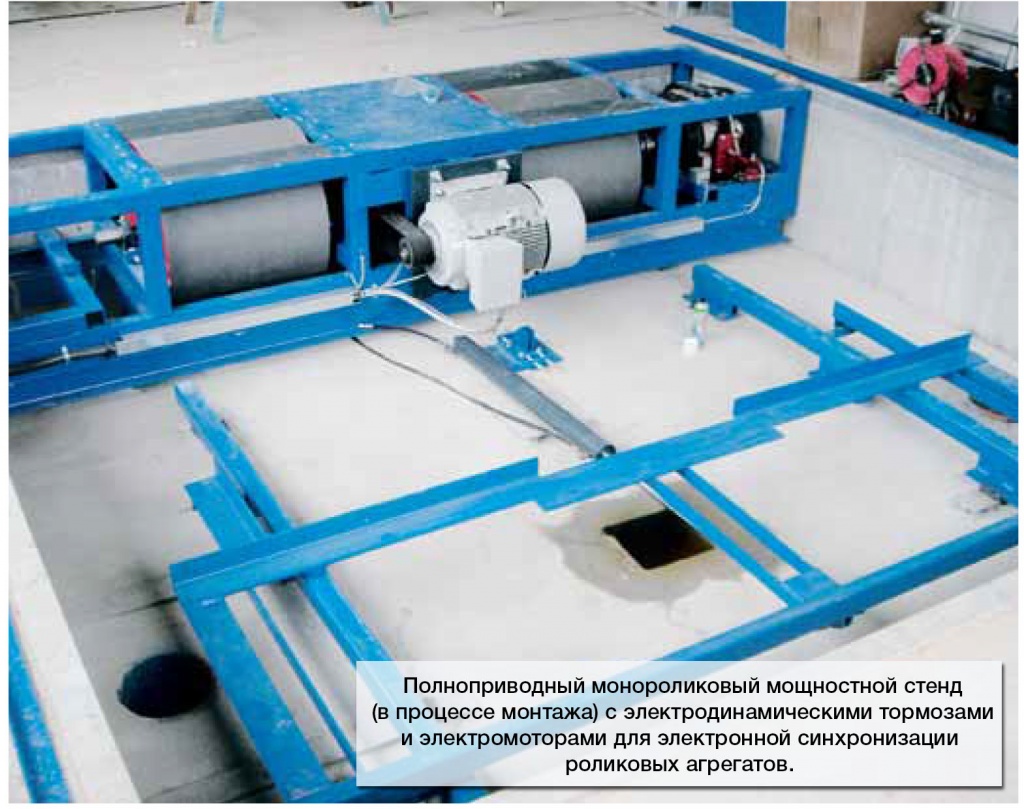
В случае полноприводных динамометров с переменным межосевым расстоянием и механической связью между роликовыми агрегатами число возможных неисправностей возрастает с дополнительными затратами на разработку. Износ подшипников, редукторов и шлицевых валов, например, а также неизбежные допуски на размеры, присущие ременным передачам, приводят к таким системам, которые даже близко не соответствуют необходимым требованиям к современной автомобильной диагностической технике.
В области современных точных процедур мощностных и экологических испытаний автомобилей со сложными системами полного привода, в том числе с электронным управлением, в интересах точности и эксплуатационной безопасности необходимо избегать каких-либо абсолютно непредсказуемых возмущающих переменных. В случае полноприводных мощностных стендов без синхронизации роликовых агрегатов это может привести к повреждению полноприводной трансмиссии автомобиля. Электронная синхронизация устраняет эту опасность в принципе, а также позволяет обеспечивать большие диапазоны изменения межосевого расстояния для соответствия самым малым и большим колесным базам автомобилей. Механические устройства синхронизации накладывают большие ограничения в этом смысле.
Понимая дальнейшее развитие автомобильной техники, высококлассные производители гаражного оборудования часто оборудуют полноприводные мощностные стенды не только электродинамическими тормозами, но и приводными электродвигателями с электронным регулированием, что позволяет адаптировать систему управления стендом к любому типу полноприводной трансмиссии - без подверженных неисправностям механических связей между роликовыми агрегатами.
Принципы симуляции дорожной нагрузки
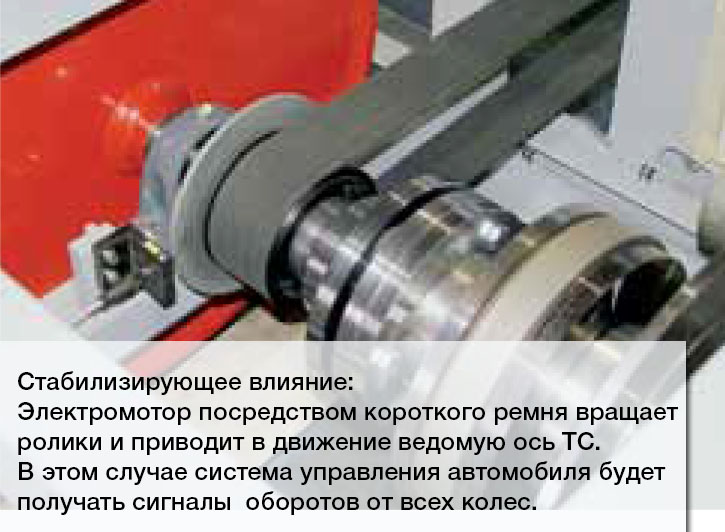
Сами по себе нагружающие колеса автомобиля ролики сами по себе не являются динамометром. В дополнение к сложной технологии измерения также требуется некоторая математика, принимающая во внимание рассмотренные выше влияющие переменные (и многое другое). Визуально все выглядит так, что при измерении мощности, экологических и других параметров, напрямую влияющих на привод автомобиля, автомобиль неподвижен, в то время как движется «дорога».
Двигатель вращает колеса неподвижного транспортного средства. При наличии достаточной силы трения приводится в движение в обратном направлении расположенное под колесом пятно контакта. Конечно, этот тип моделирования движения технически непрактичен, поэтому (функционально) динамометр обычно имеет пары роликов, колеса оси автомобиля располагаются между этими роликами.
Как объяснялось выше, принцип может быть модифицирован – колеса могут располагаться на вершинах больших роликов, а не между двумя роликами меньшего диаметра. Тем не менее, это не имеет значения для следующих основных объяснений:
Движущая сила FA колес производит:
1. Ускорение a и изменение скорости Δv транспортного средства с массой m.
F1[Н] = m[кг] · a[м/с2]
Произведение массы m в килограммах и ускорения а в метрах в секунду за секунду дает движущую силу в ньютонах.
2. Изменение градиента автомобиля при движении в гору.
F2[Н] = m[кг] · g[м/с2] · sin a
3. Преодоление сопротивления движению.
F3[Н] = FWheels + FAir
• с сопротивлением качению шин и коэффициентом деформации шины µr и µW колес:
FWheels = µFG = (µr + µW) · m · g
• с сопротивлением воздуха: Fair = ½ ρ cW Av2
где: ρ = удельная плотность окружающего воздуха
cW = коэффициент лобового сопротивления
A = площадь поперечного сечения автомобиля
v = скорость воздушного потока
• F3 зависит от скорости
Результат: Когда движущая сила FA разгоняет автомобиль прямо вперед с постоянной скоростью V, справедливо следующее выражение:
FA = F3
Если движущая сила FA ускоряет автомобиль в гору, все три силы объединяются и справедливо следующее выражение:
FA = F1+ F2 + F3
Движущая сила FM двигателя передается на колеса через кривошипы и валы (т.е. “с помощью” крутящего момента). При этом должно быть преодолено внутреннее сопротивление, определяемое по большей части трансмиссией и подшипниками. Часть исходной силы (если смотреть от сцепления), таким образом, теряется в приводе автомобиля. FM = FV + FA (где FV - сила, необходимая для преодоления внутреннего сопротивления).
Если движущая сила двигателя FM прикладывается на определенном пути, то на этом пути совершается работа WM.
При этом транспортное средство использует энергию:
WM [Нм]= FM [H]· s [м]
где s = пройденное расстояние в метрах
Работа WM производится для:
• увеличения кинетической энергии транспортного средства при ускорении на расстоянии s.
W1= F1 × s = m (Δv)2
• увеличения потенциальной энергии транспортного средства при движении в гору.
W2= F2 × s = m×g×h
• преодоления сопротивления движению на участке пути s.
W3= F3 × s
• преодоления внутреннего сопротивления автомобиля.
W4= Wv= FW × s
Полная работа, которую должен совершить двигатель:
WM = W1 + W2 + W3 + W4 = WA + WV
Если работа W выполняется в течение периода времени Δt, мощность за время Δt составит:

(где v является средней скоростью движения за время Δt).
Если мы возьмем малые времена Δt и знаем движущую силу FA в любое время t при движении, мы можем определить движущую силу в любое время следующим образом:
PA (t)= FA (t) × v (t)
Эффективная мощность двигателя на сцеплении в таком случае составит:
Эффективная мощность двигателя PM представляет собой сумму движущей силы PA и мощность рассеяния или мощность механических потерь PV.
Ролики, приводимые в движение автомобилем, могут затормаживаться с помощью регулируемого усилия FB, которое создается соответствующим устройством стенда.
Таким же образом, соответствующие (моделируемые) скорость и ускорение транспортного средства могут быть рассчитаны из частоты вращения и изменений частоты вращения, измеренных на роликах стенда.
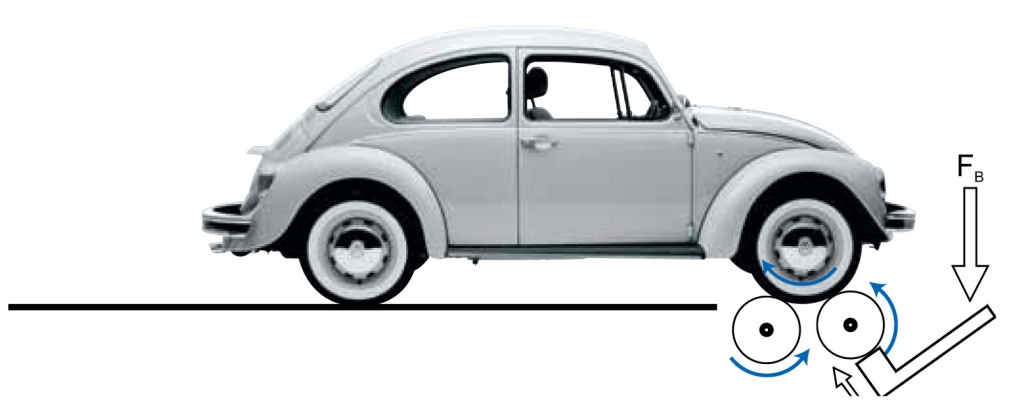
И инерция приводных роликов и регулируемое тормозное усилие FB влияют на движущую силу FA. В то время как инерция масс роликов противодействует движущей силе в прямом соответствии с переменными движения (частота вращения, изменения частоты вращения), тормозные силы электродинамических тормозов могут быть установлены точно при помощи управляющих напряжений.
Таким образом для реалистичного моделирования движения автомобиля необходимо воспроизводить в правильной пропорции все силы, противодействующие приводу автомобиля, для каждого состояния движения.